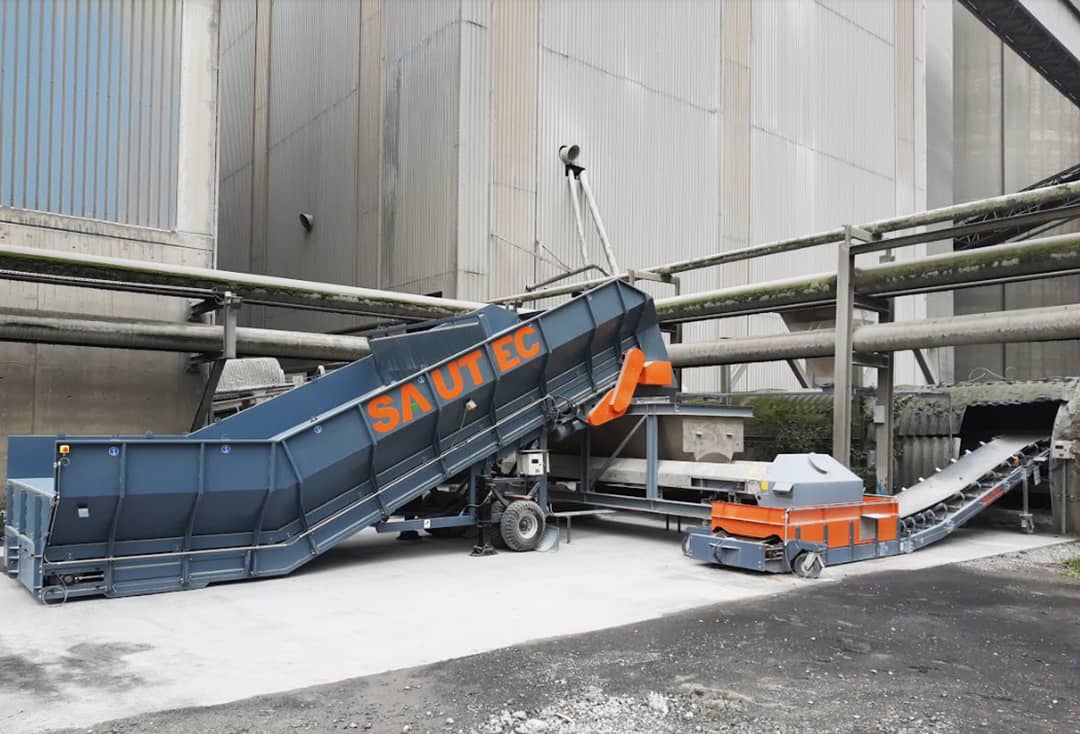
The energy crisis and the increase in energy prices are giving a real boost to the energy transition, particularly in the energy-intensive industry.
More and more of you are looking for alternative solutions, both to replace fossil fuels and to meet the low-carbon challenge.
It is therefore important that you are able to implement alternative solutions immediately, with significant effects on the decarbonisation of your business while continuing to meet the demands of your customers.
In this article, we show you how we have enabled two of our customers to quickly implement changes to their manufacturing processes, test new solutions and achieve rapid results, thanks to adaptable solutions that fit into existing facilities.
Case 1: a temporary rental solution for quick results.
Recently, coal-fired power plants have been back in operation in Europe. This is particularly true for the Cordemais thermal power plant (France) which, since this winter, has been running at full capacity to support and meet the demand for electricity.
In order to maintain its activity while decarbonising its electricity production, a project to convert the plant has been launched. This project, called “Ecocombust”, aims to convert the thermal power plant into a biomass power plant.
Among the many challenges of the project, there is the rapid replacement of 20% of the coal burned with pellets by the winter of 2023-2024. After a study with the client on the possibilities that could be implemented, the installation of a temporary conveyor system to feed pellets to a biomass converted mill turned out to be the best option.
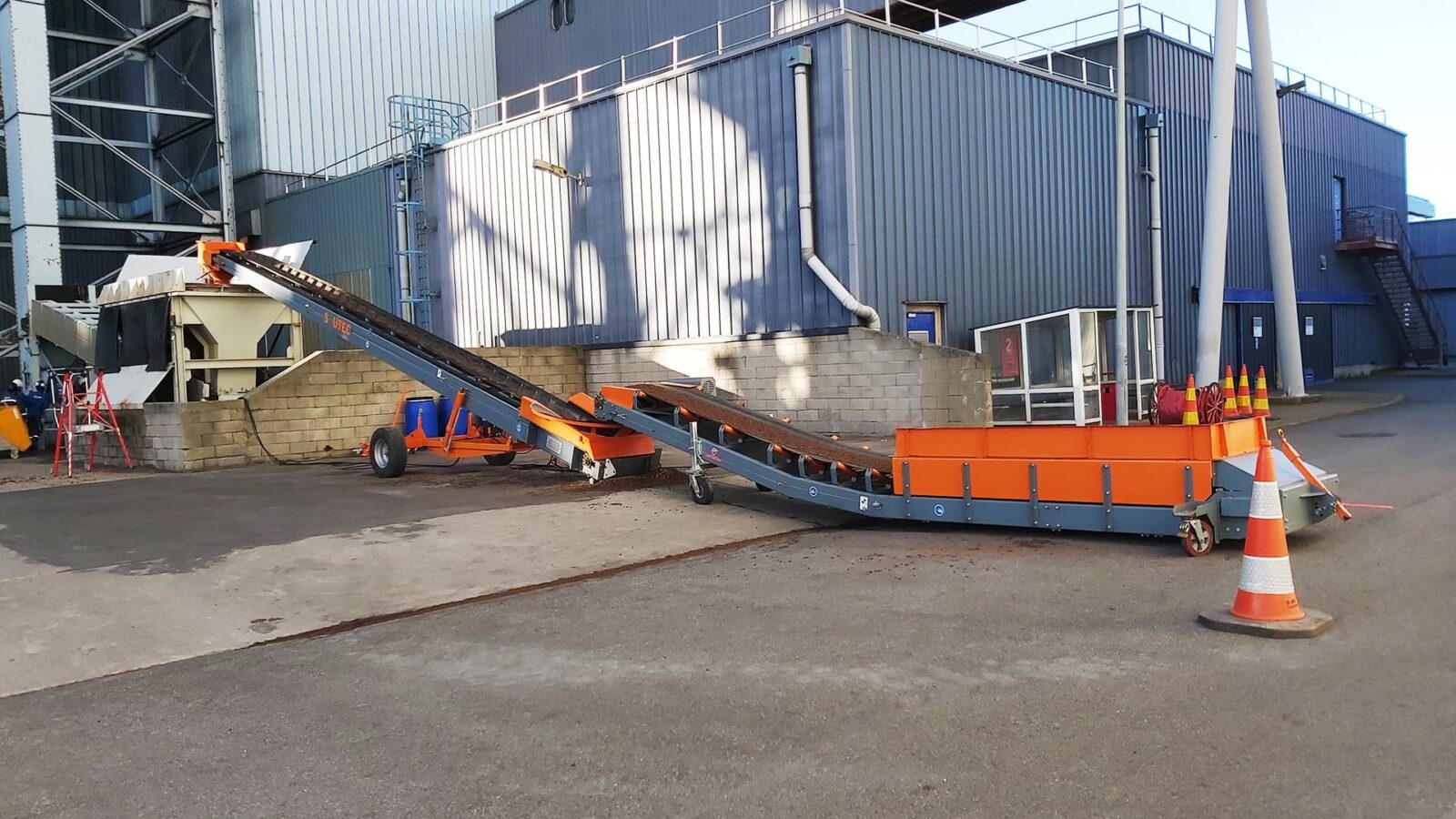
The aim was to provide the customer with maximum flexibility.
The conveying solution we delivered to the thermal power plant consists of a truck unloader and a belt conveyor. These are two mobile systems that can be easily positioned to adapt to the constraints of the site.
In this case, the equipment allows the customer to unload the pellets from the semi-trailers and transfer them in a continuous flow into a hopper located 3 metres high. The conveying solution is simple and easy to implement and does not require any civil engineering.
The proposed solution is temporary. However, it should not be a constraint. The major advantage of the power plant is its ability to increase or decrease electricity production “on demand”. It was therefore important to us that the customer could find this flexibility in the temporary conveyor solution we provided.
From the rental service to the design of our equipment, we want to provide our customers with maximum flexibility. Depending on the tests carried out and the progress of the work, the plant can, if necessary, extend the rental period and move the equipment into its site for further tests.
In this way, the power plant benefits from the flexibility to achieve its initial objectives while at the same time carrying out the work necessary to benefit from a permanent solution with greater capacity.
Case 2: equipment that improves the existing installation.
The cement industry is a major emitter of greenhouse gases and has also been seeking to reduce its impact on the environment for several years. One of the possible levers is to reduce the clinker content in cement production by integrating substitute materials.
This is one of the ways being explored by a major client cement plant, by integrating combustion ashes into its manufacturing formulas.
In this type of project, it is important that the installation can adapt to the client’s changing needs. Today, our customer wants to receive and handle ashes. In the future, it could concern other materials.
For this reason, the cement plant wanted to benefit from versatile equipment able to integrating and complementing the existing installation. These characteristics are part of the raison d’être of our equipment range.
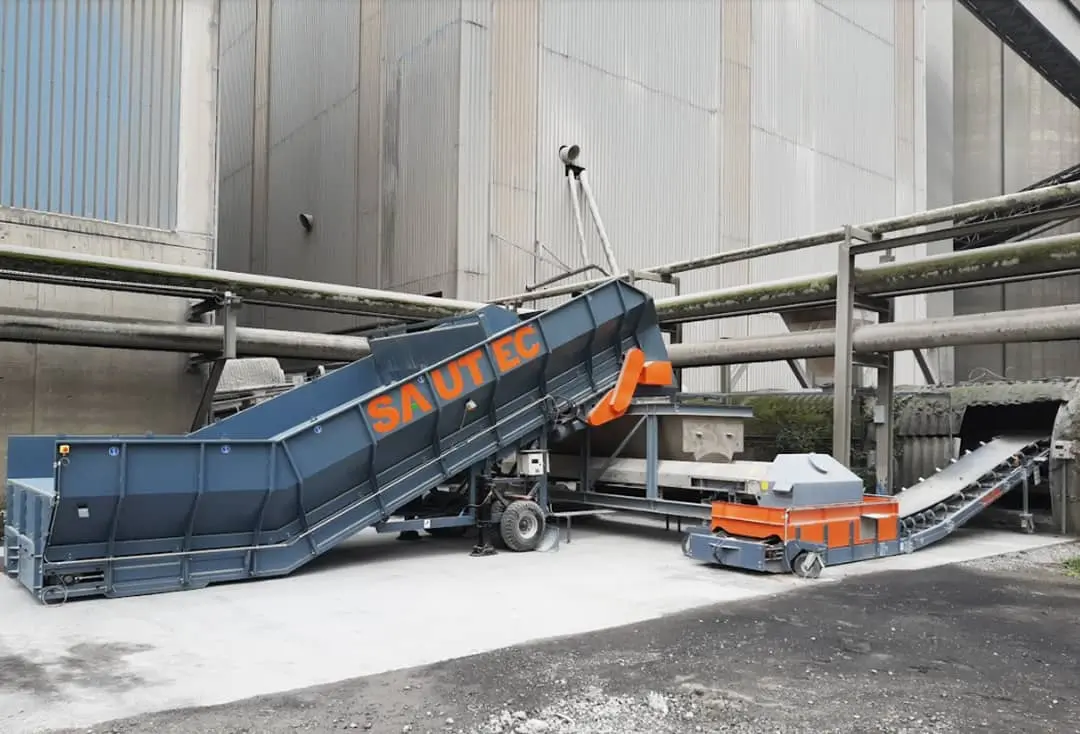
The response to the customer’s need was the supply of a custom-made unloading hopper and truck unloader. Without modifying the site installation, and without any civil engineering, the cement plant is now able to quickly receive the ashes arriving by truck and integrate them into its manufacturing process.
Indeed, after receiving the ashes, the hopper feeds an existing dosing conveyor. After passing through this dosing conveyor, the ashes are received by the truck unloader and transferred to a conveyor belt a few metres further on.
Ultimately, the entire production chain is improved.
No doubt that projects and needs like these will increase in the months and years to come. We are at your disposal to assist you in your decarbonisation projects.