Simplified bag storage thanks to custom-made conveyors.
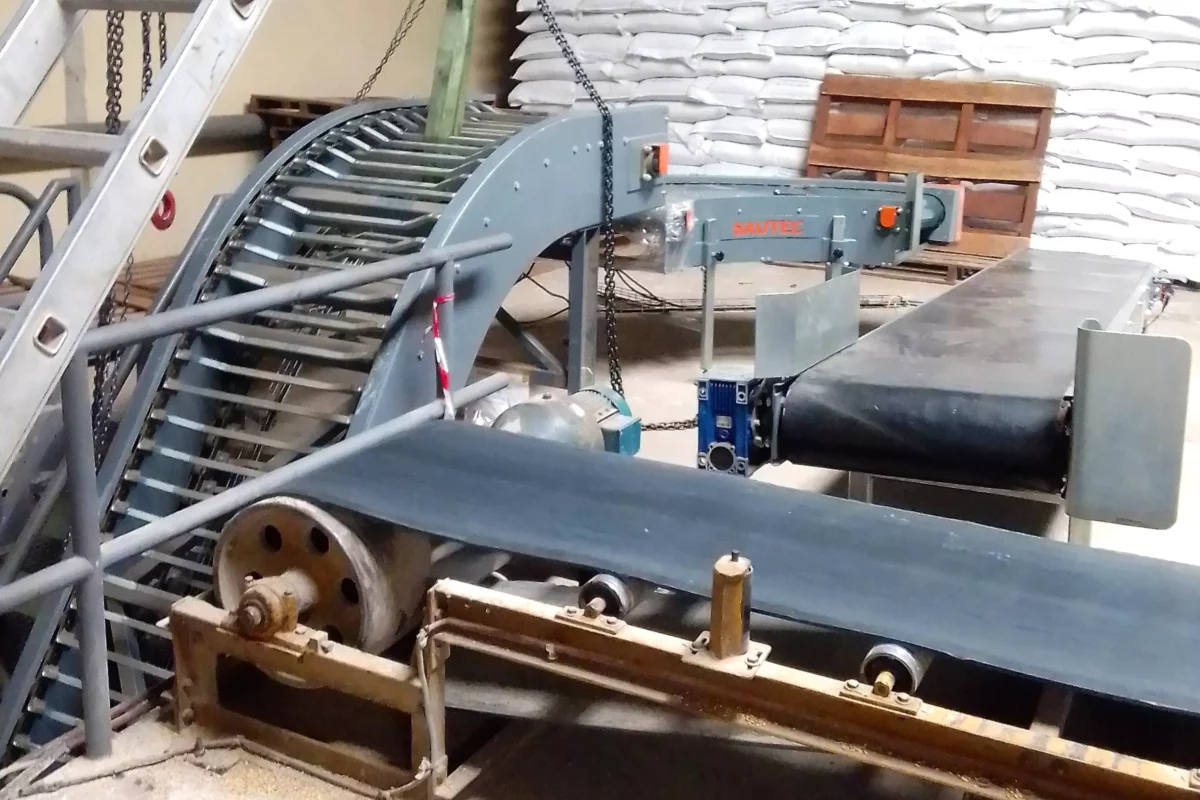
Feedback from a project carried out for a major player in the brewing industry in the Democratic Republic of the Congo. To improve the flow of raw materials and their storage, we were contacted for the manufacture of custom-made conveyors. A solution that was essential to the success of the warehouse reorganisation project and our customer’s desire to optimise its bag handling operations.
Context and challenges.
The client’s problem was managing the flow of raw materials in bags, stored on the first floor of a warehouse. The use of a single, ageing elevator belt for lifting and lowering the bags was no longer adequate to absorb the deliveries of raw materials and meet the plant’s production capacity.
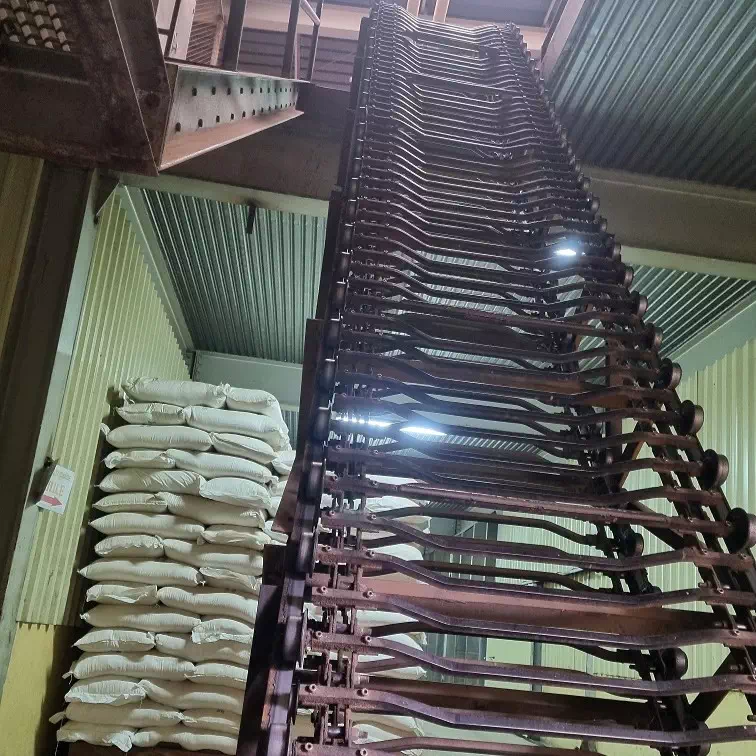
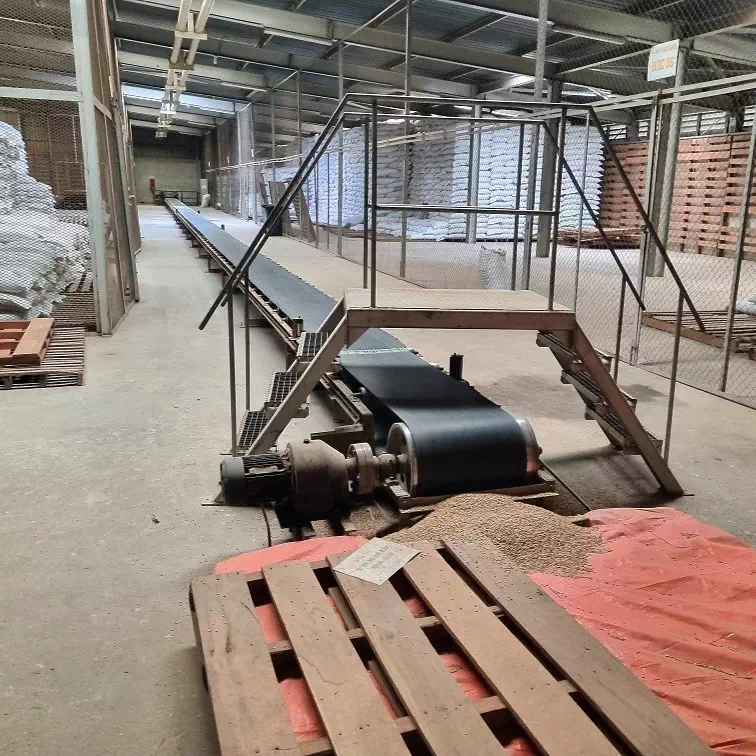
On the upper floor, there is a fixed transfer conveyor whose role is to transport the bags to the required storage area and to facilitate destocking.
To resolve this situation, the customer created a second access to the storage floor so as to have one access dedicated to the ascent of the bags and another to the descent of the bags.
For these reasons, we were asked to design and install two separate elevators – one for incoming flows, the other for outgoing flows – in perfect harmony with the constraints of the building and ensuring their connection with the transfer conveyor already in place.
Solutions delivered.
To meet the customer’s requirements, we designed and manufactured two completely tailor-made fixed installations:
Installation 1
A chain elevator belt dedicated to the ascent of the bags, positioned at the new access door, complemented by a curved conveyor and a straight conveyor to optimally orientate the bags on the existing fixed transfer conveyor.
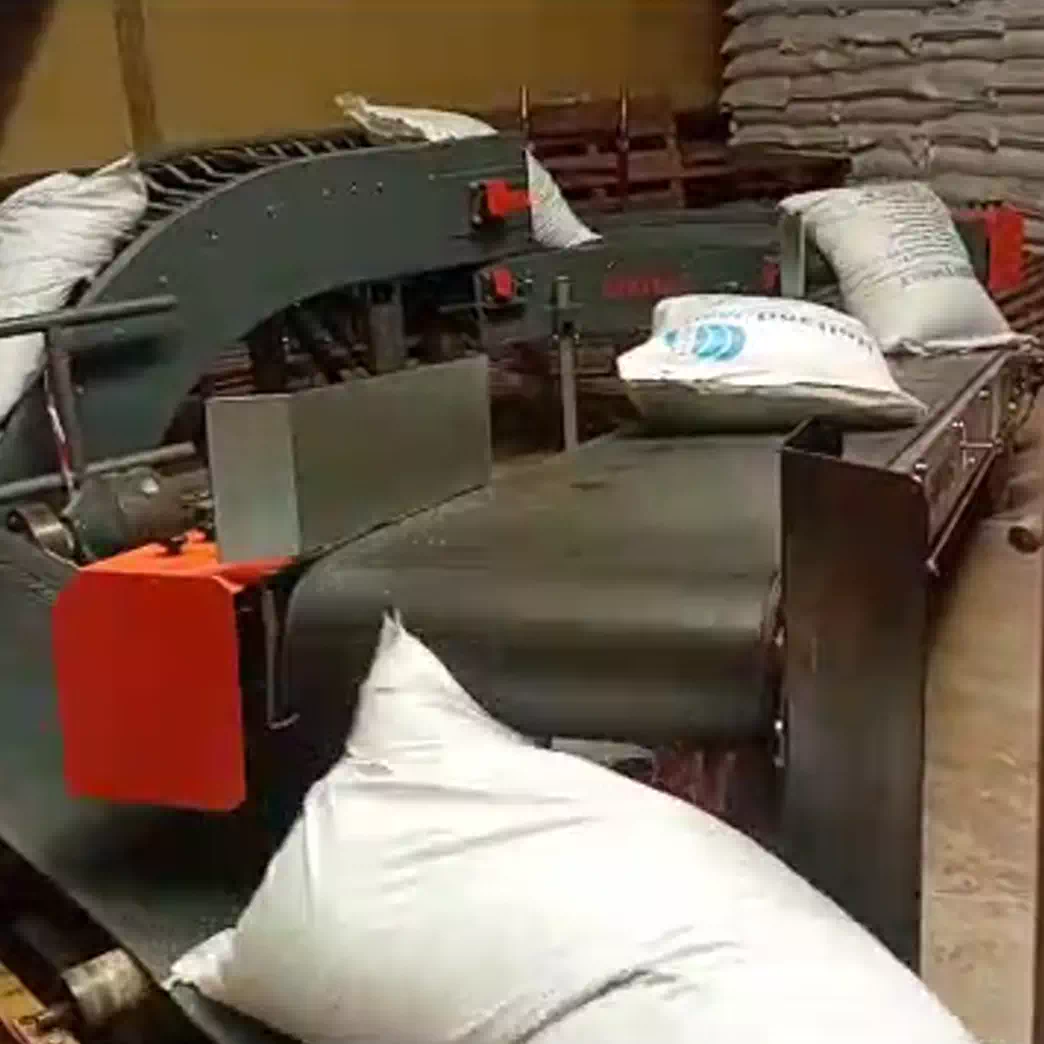
Installation 2
A second chain elevator for ensure the smooth descent of the bags from the transfer conveyor to the ground floor to supply the production lines.
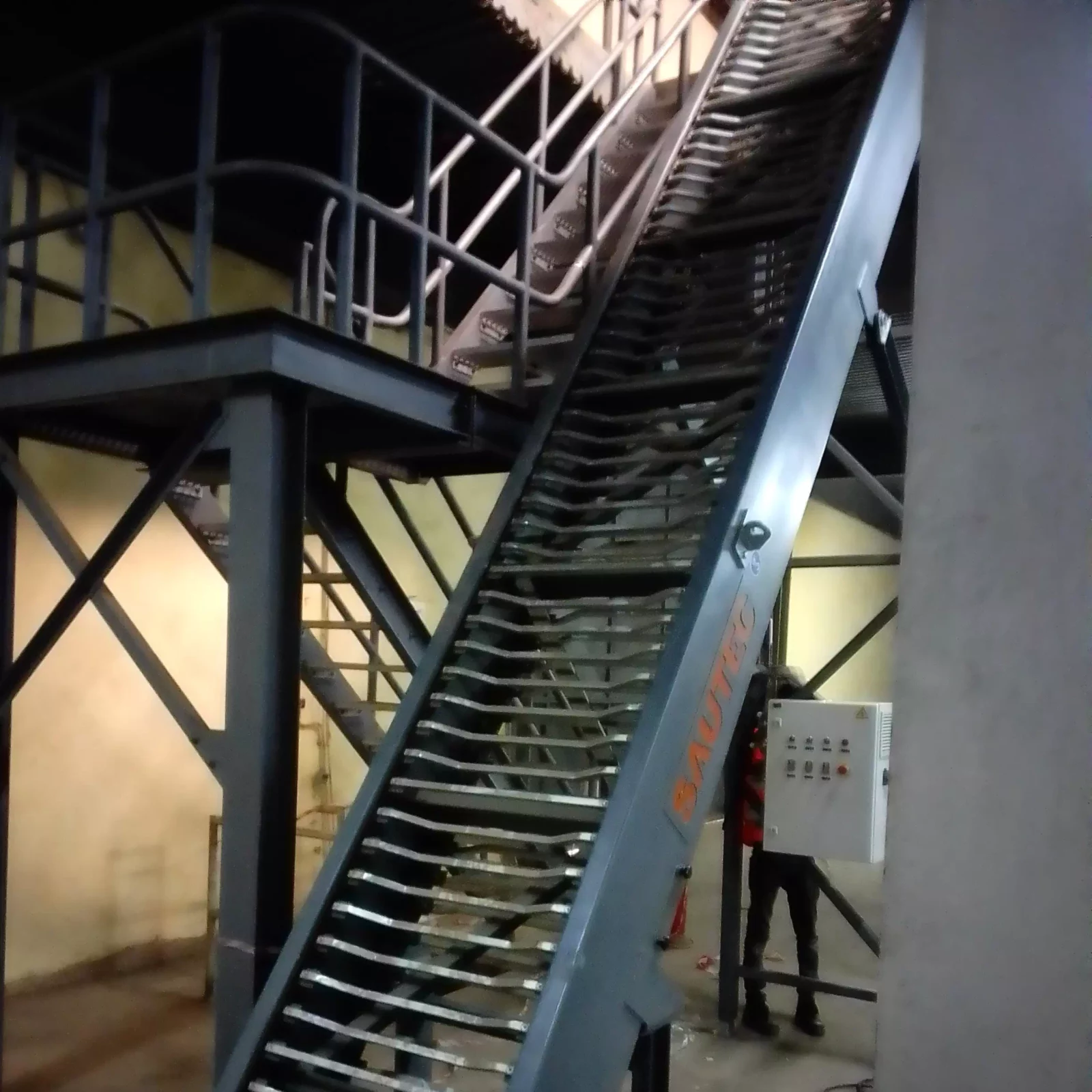
Implementation.
Our approach was built around close collaboration with the customer. After an initial remote consultation to establish precise expectations, our business manager based in Cameroon visited the site. This visit enabled us to analyse the requirements in detail, study the technical constraints and carry out the required site measurements.
This approach enabled us to produce a complete offer, including an analysis of requirements, detailed plans and a 3D simulation of the future installations.
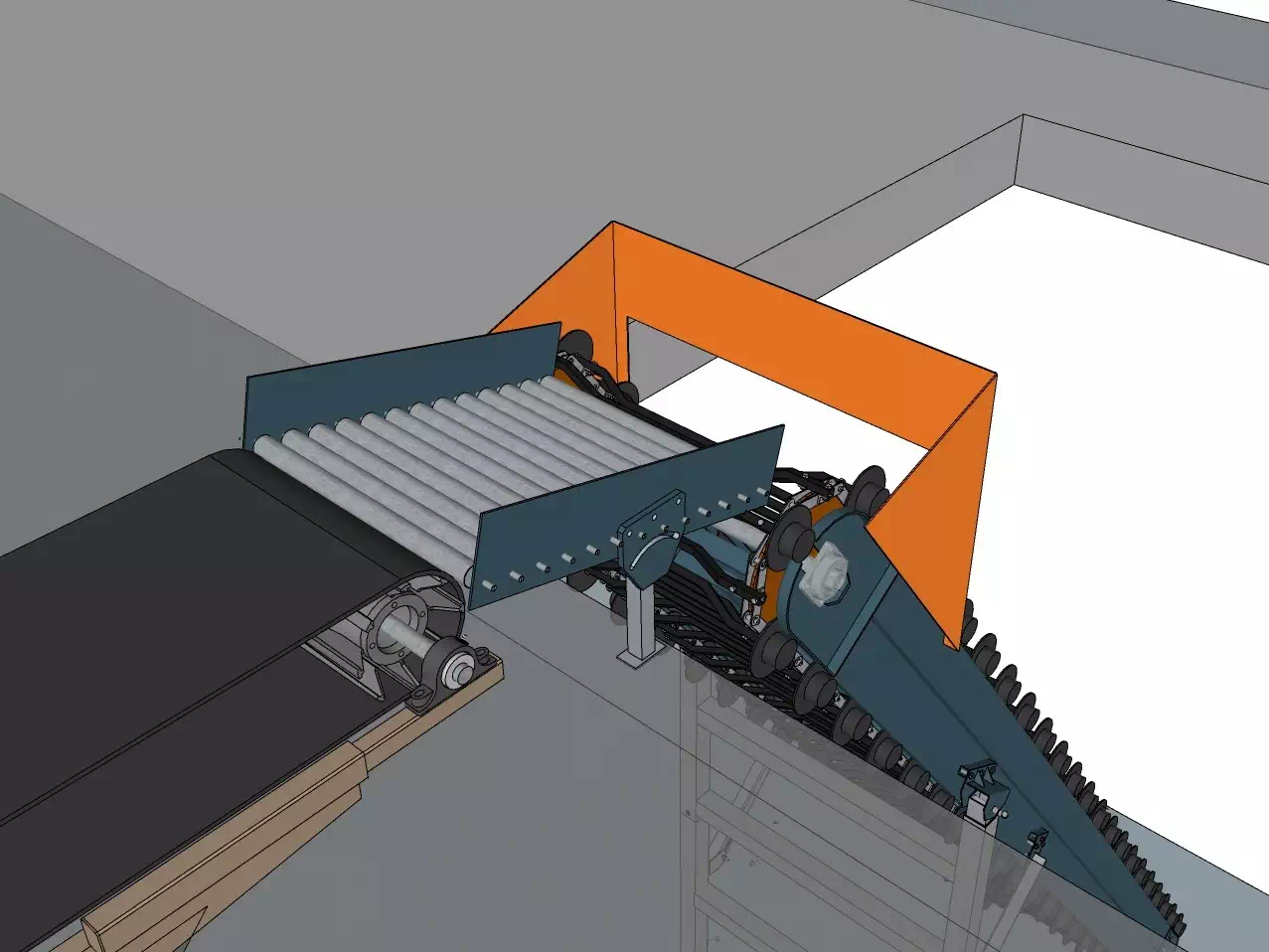
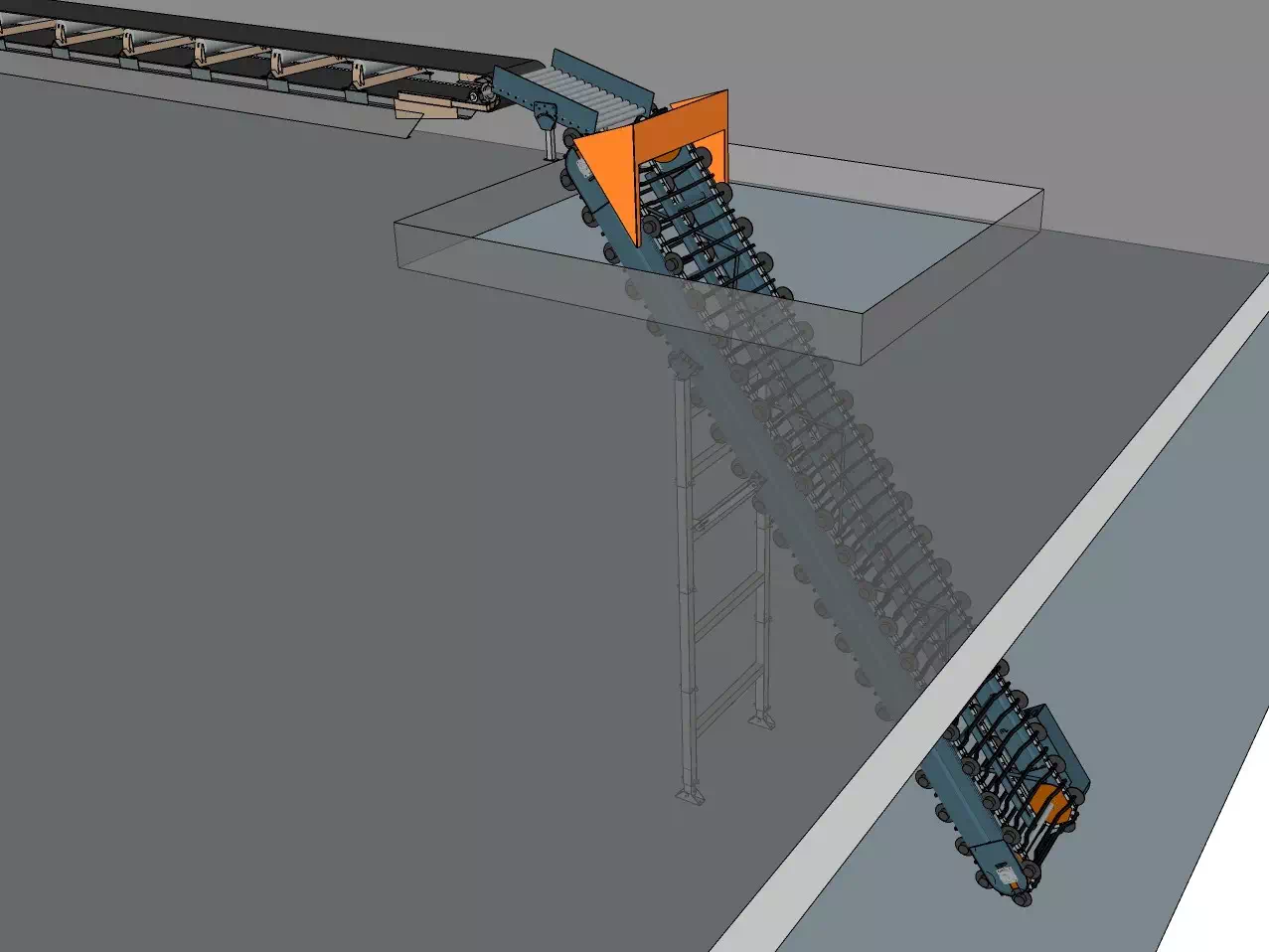
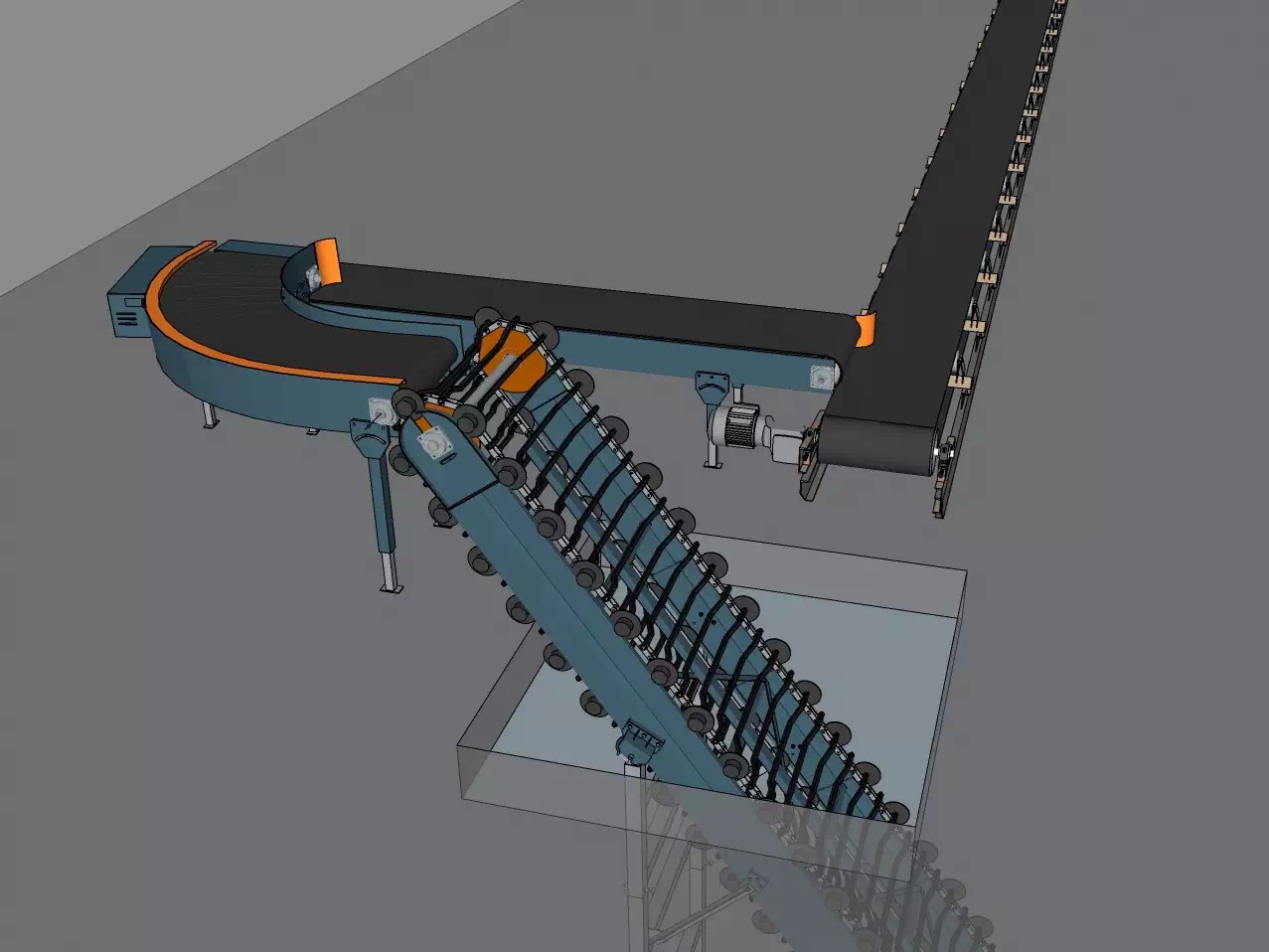
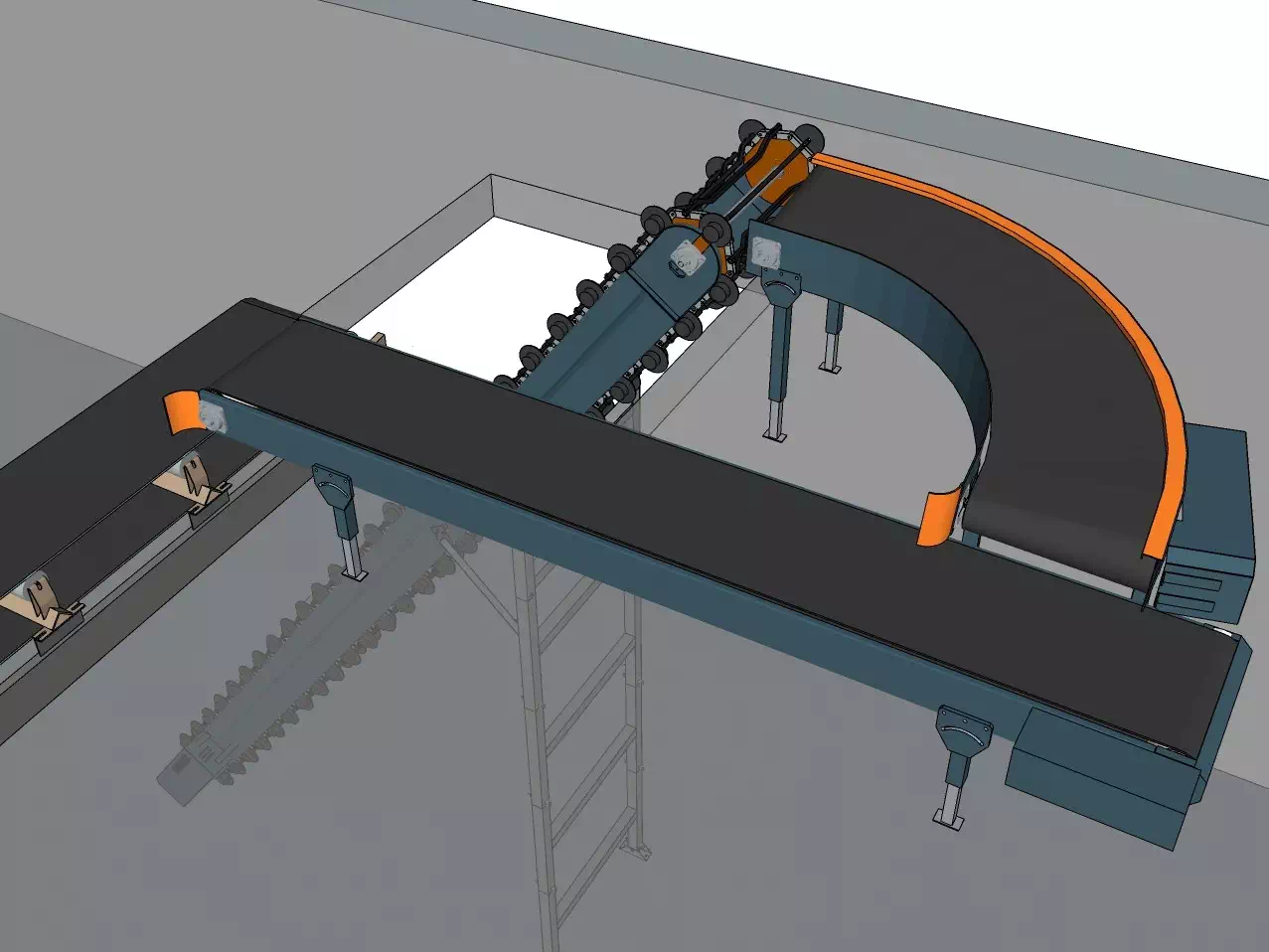
Once the project had been validated and the equipment delivered, our business manager and a technician went on site to carry out the installation (supported by 4 members of the customer’s staff), start-up the equipment and train the operators in the settings and maintenance of the new equipment. It took several days to complete all these operations and ensure a transfer of skills to the local teams.
Benefits and results.
This collaboration enabled the customer to achieve significant improvements in the site’s logistics organisation. The clear separation of incoming and outgoing flows has considerably improved the efficiency of operations. Raw materials are now received and retrieved smoothly and without interference, optimising the supply of production lines.
The equipment installed is robust and perfectly adapted to intensive industrial use. Their custom-made design carefully respects the constraints of the site, while offering simplified maintenance and easy access to spare parts, thus guaranteeing the longevity of the installations.
Faced with the growing challenges of industrial logistics, optimising production flows is becoming a major issue.
We’re here to listen to your needs and offer bag handling solutions tailored to your specific requirements. By entrusting us with your project, you benefit from our expertise in turning your logistical challenges into opportunities.