Conveyor belts: the flexible solution for earthworks.
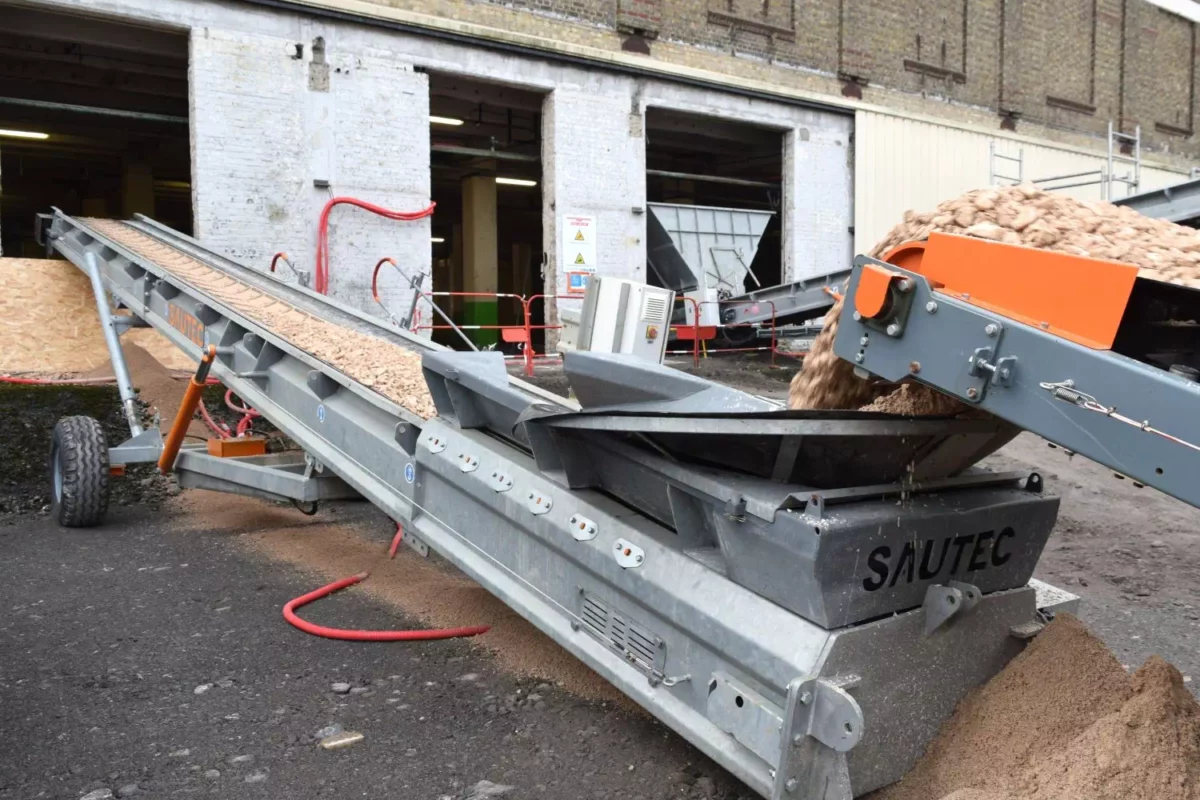
For a warehouse renovation work, earthworks need to be carried out indoors. The configuration of the site makes it difficult to use construction machinery to remove rubble and transport backfill materials. In this context, transferring materials is a challenge. But that’s exactly what our customer has achieved by using conveyor belts as a complementary solution to site machinery.
Context and challenges.
A company specialising in structural work was commissioned to renovate the floor of a warehouse. Over time, the storage of heavy loads has subsided and deformed the ground, making storage difficult. One of the stages of the construction site involves excavating the entire surface of the building to a depth of one metre. In total, there are more than 900m3 of rubble to be evacuated and just as much backfill material to be transported.
The main constraint is the configuration of the site. Despite the creation of openings to allow the passage of site machinery, the interior space is restricted and confined.
For safety reasons, it was desirable to limit machine traffic as much as possible, and therefore material handling operations.
Our customer was looking for a solution to evacuate and transfer materials in a way that was optimised and safe for site teams.
Proposed solution.
To meet this challenge, we proposed a conveying solution composed of 3 pieces of equipment:
A 14-metre site conveyor to remove rubble. Positioned inside the building, it evacuates the rubble to a skip located outside. A hopper has been installed on the conveyor to make it easier to dump the rubble onto the loader. To compensate for the height of the embankment, the conveyor was installed on two concrete blocks.
To receive and supply the backfill material, a 7-metre truck unloader and a 12-metre site conveyor were installed. The truck unloader enables material to be received through the skip hatches and then transferred in a regular flow to the site conveyor. The conveyor then transports the material through a window into the building.
Thanks to this simple installation, our client was able to set up an operating mode that reduces the handling of material. The whole thing thus creates an efficient and secure circuit for the evacuation and supply of rubble and sand.
A turnkey installation.
The conveyor belts are delivered assembled to the site by flatbed truck. To ensure that the equipment was installed quickly and efficiently, the customer opted for our commissioning assistance service. This turnkey service ensures that a SAUTEC technician is on hand when the equipment is received to:
- Coordinate the unloading and installation of the equipment
- Supervise commissioning
- Ensure that the installation is compliant and safe
- Advise the teams on the best use of the equipment
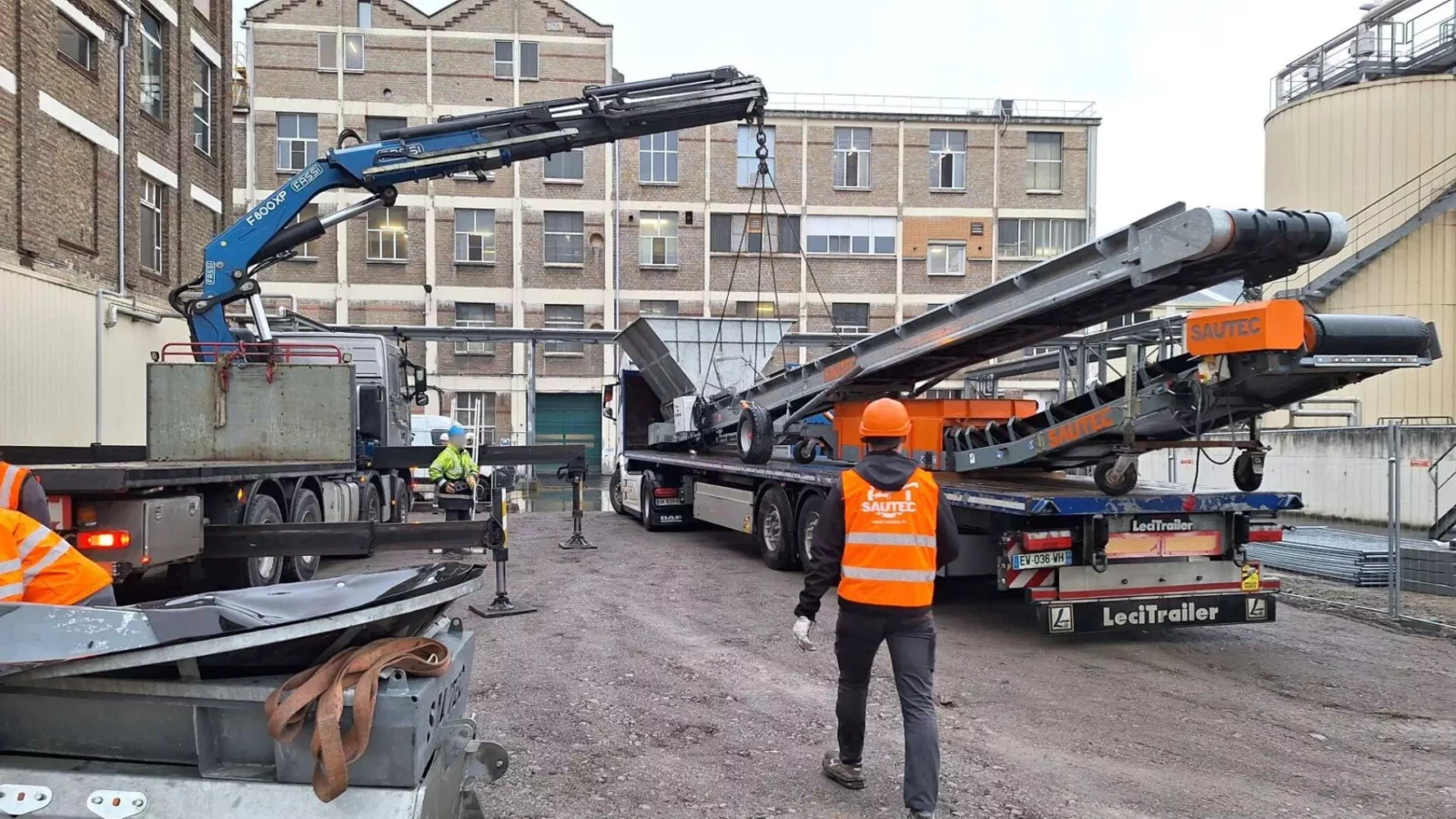
This support enabled the customer to concentrate calmly on its core business and start work on the site without losing any time.
A tangible benefits
The installation of conveyor belts on the site has produced results in 3 areas: operational efficiency, safety and environmental impact.
- The conveyor belts made it possible to evacuate and transport material in a continuous, safe flow at optimum speed. The unloading of 30 tonnes of backfill material and its transfer to the work area is completed in 20 minutes.
- In terms of safety, the use of conveyor belts has considerably reduced the need for site machinery to come and go to handle the material, thereby reducing the risk of accidents.
- Finally, conveyor belts have the enormous advantage of using electrical energy and therefore emitting no exhaust fumes. As well as reducing the site’s carbon footprint, the use of conveyor belts has also helped to maintain acceptable air quality for the staff working inside the building.
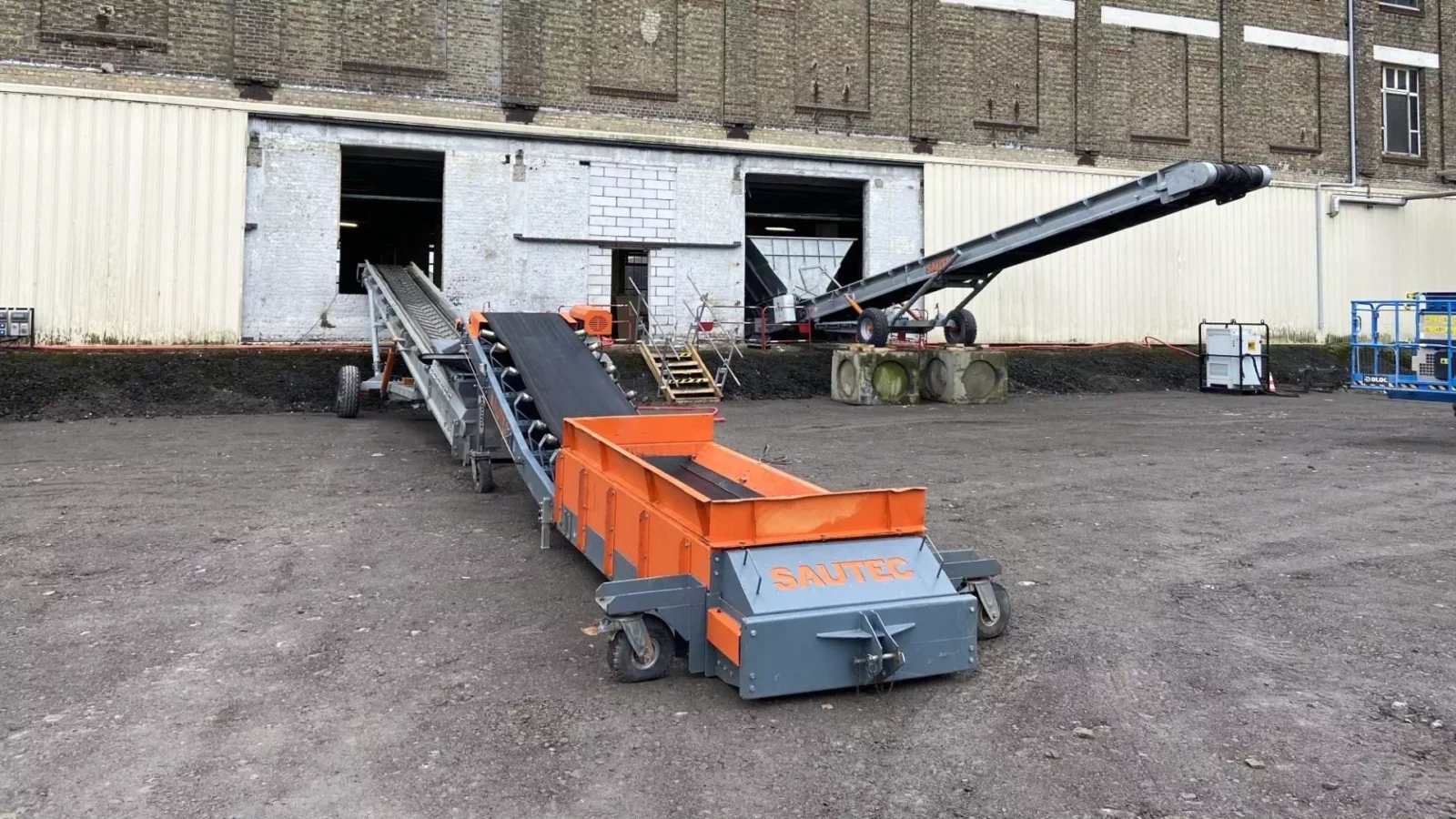
Do you too have an earthmoving or materials transfer project in a difficult-to-access environment? Would you like more information about our solutions? Then get in touch with us!