Cocoa exporters: load and weigh your containers independently.
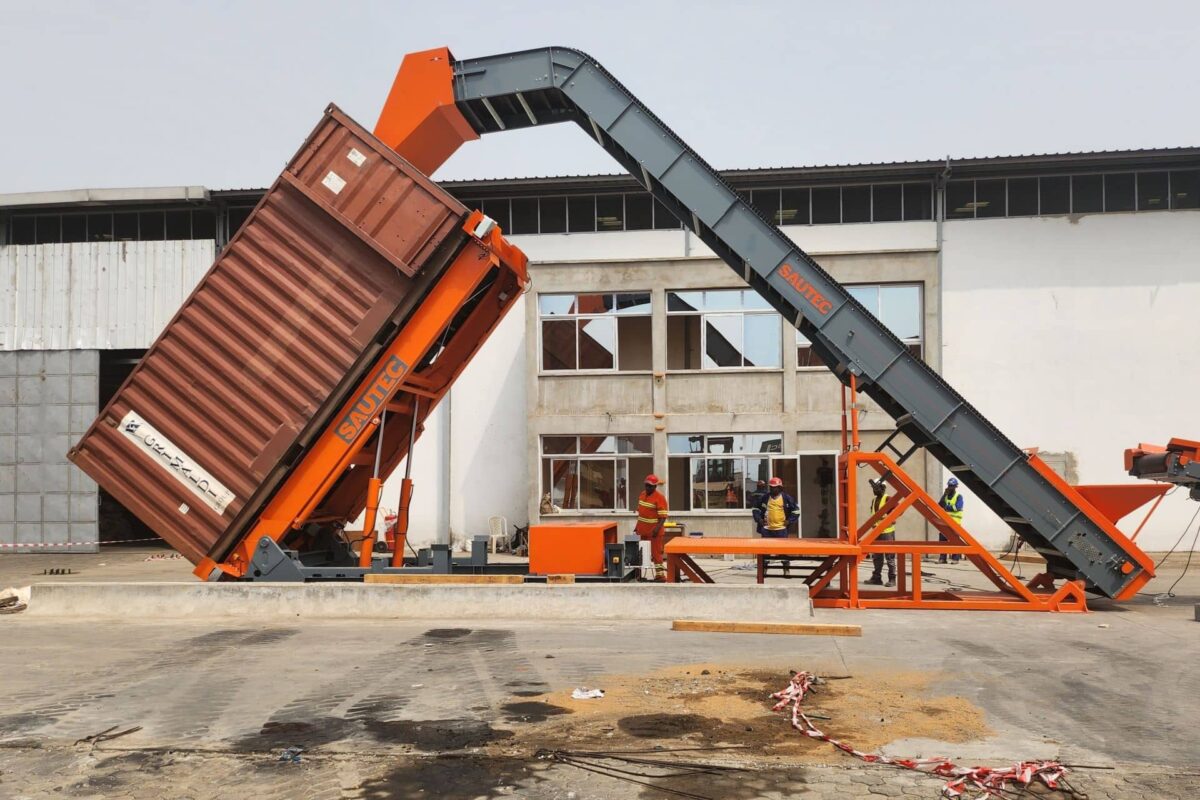
The case of a Cameroonian cocoa exporter.
The export of agricultural products, such as cocoa, is a crucial sector for many countries, notably Ivory Coast and Cameroon. However, port congestion during the high season, the need to preserve product quality and the risk of theft or loss of goods are recurring problems. The complexity of operations involving many different service providers adds further pressure to remain competitive.
In response to these challenges, Cameroon’s leading cocoa exporter has equipped itself with a bulk loading station equipped with an integrated weighing system.
The aim is to gain greater autonomy and speed in handling operations, by eliminating the need to call on service providers for loading and weighing.
Solution implemented.
The bulk loading station is a complete solution for controlling the logistics chain, from cutting the cocoa bags to loading the sea containers. It includes an area where several operators can cut the bags, an elevator belt and a container tipper.
The container tipper is an hydraulic equipment that tilts 20‘ and 40’ containers. Here, the version delivered to the Cameroonian customer is configured to tilt 20-foot containers at 50°. The weighing system was integrated as an add-on module to avoid any mechanical modifications and keep the solution simple.
To enable weighing, the container tipper was attached to 4 high-strength mounting kits. Each kit can support a load of 15 tonnes. There was no need to build a platform between the mounting kits and the dumper, with the dumper chassis acting as the platform.
This configuration is less costly and easier for the customer to clean, while still being designed to withstand movement, shock and vibration during container filling.
How the loading station works?
The loading system can be operated manually or automatically. A remote-control box is used to control the loading station and receive weighing data. This mode of operation simplifies the container loading process, while ensuring that the safety requirements are met.
- The automatic loading cycle starts when the sensors detect the presence of a container on the tipper and the twists locks are correctly locked.
- As soon as the safety conditions are verified, the hydraulic system starts and tilts the container to 50°.
- Once this position has been reached, the lift moves into position above the container, ready to receive the load, while the weighing system performs a 0 setting for accurate weight measurement.
- Once these steps have been completed, the loading conveyor and lift start up, initiating the container filling process.
- As the loading weight approaches the set threshold, the loading speed adjusts to prevent overfilling. Once the desired weight has been reached, the process stops automatically, signaling the end of loading.
Installation on customer site.
The installation took place in several steps:
- In-depth analysis of requirements on the customer’s site and preparation of plans and 3D simulations.
- Site preparation and equipment installation.
- Tests and adjustments.
- Staff training
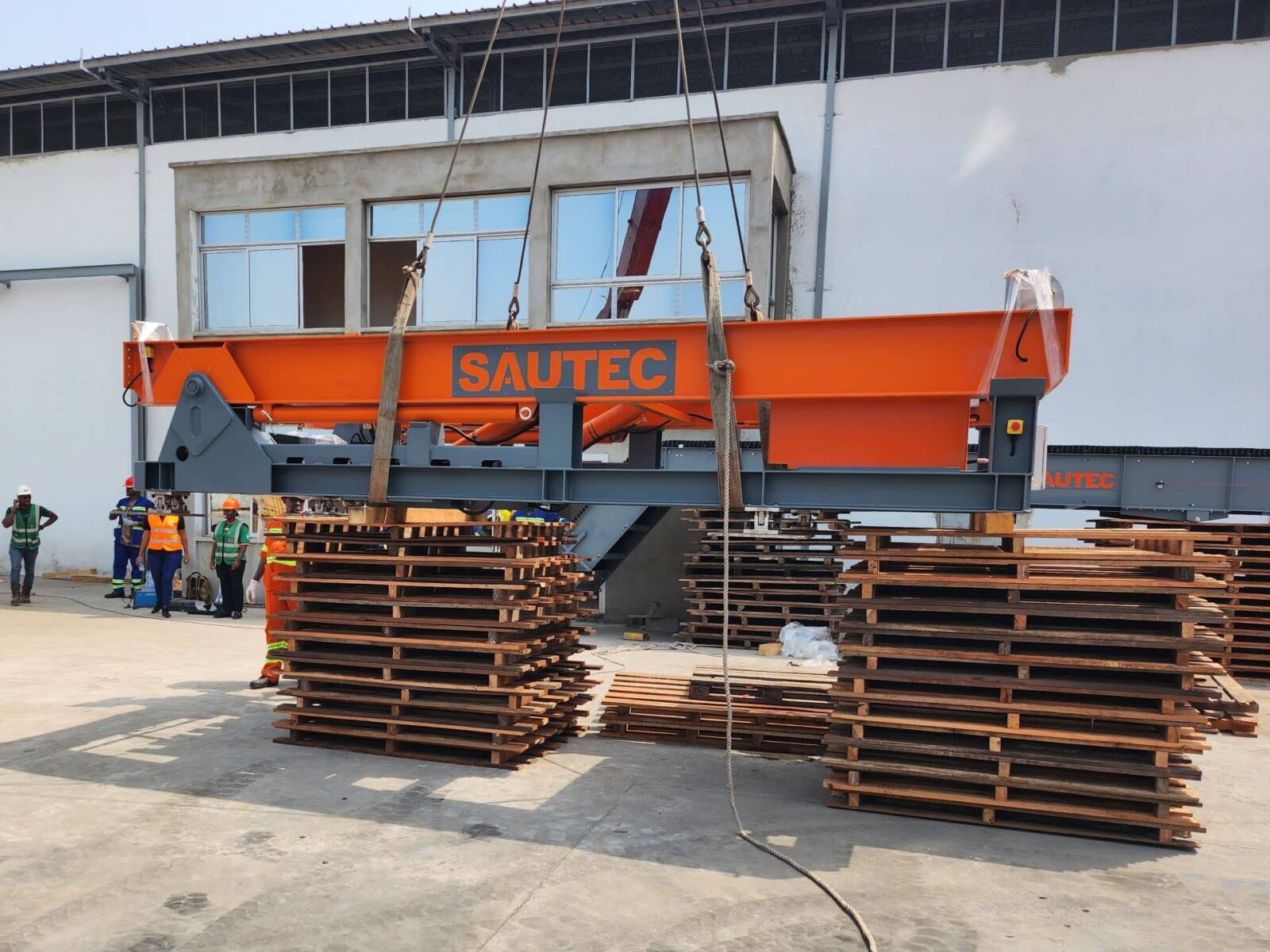
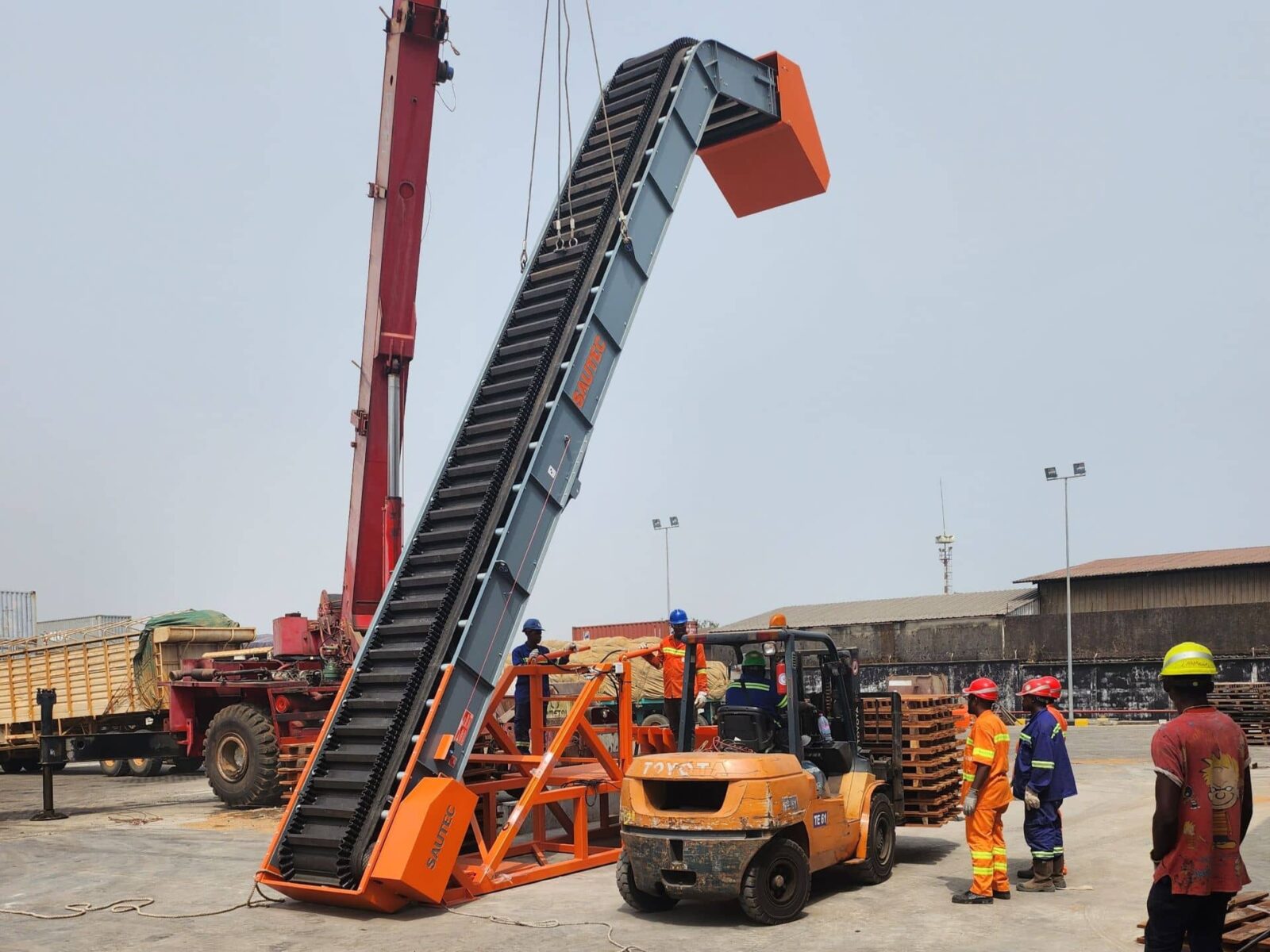
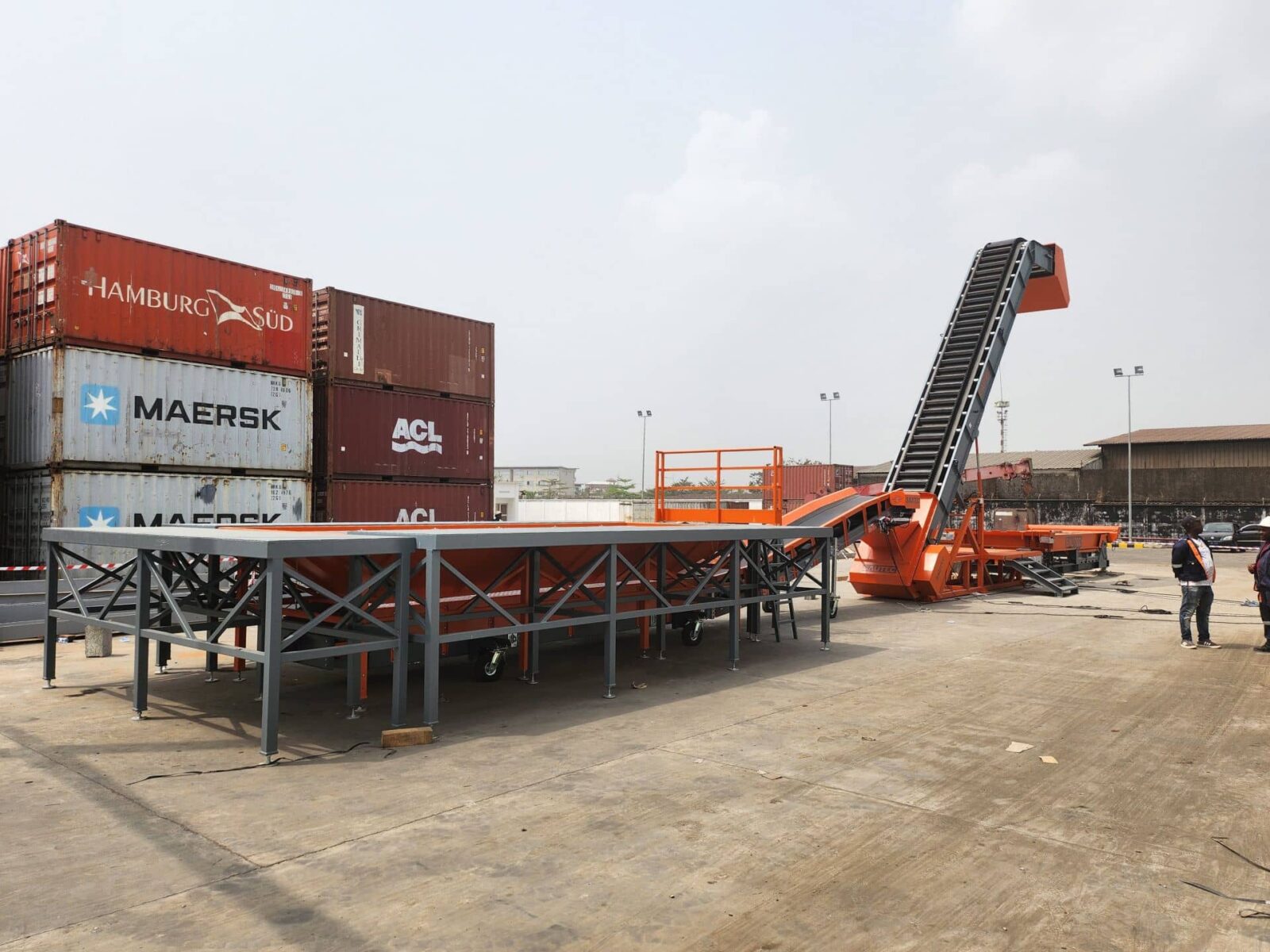
Close collaboration between our on-site team and the customer’s technical teams enabled us to adapt the solution to the needs and constraints of the site.
Benefits for the customer.
This solution has enabled the customer to save time and improve the efficiency of its handling operations, significantly reducing the logistical processes involved.
A 20-foot container can now be loaded in around twenty minutes and instantly weighed ready for shipment, giving total autonomy from bag cutting to final loading.
Like all our container loading equipment, the loading station is simple, easy to maintain and easy to move.
Do you need to improve your bulk container loading processes?
In Cameroon, Ivory Coast, Nigeria… many customers rely on us for bulk container loading. We would be delighted to discuss how our solutions could be adapted to your context. Our equipment adapts to your needs.